Kaizen Method
.jpg)
The Kaizen method completely changes the work dynamic. Interesting? Well, keep reading to learn more about him.
What is the Kaizen method?
The Kaizen Method, or, “method of continuous improvement”, was created in Japan after the Second World War, with the purpose of being at the level of Western powers in the economic sphere.
It is based on performing Small changes To achieve big improvements in the final results. It's not just about improving existing processes, but about eliminating those that, instead of contributing, are taking away from us, either because they are unnecessary or because they can be done in a much more efficient way.
Another advantage of moving forward with small steps is that it makes the change progressive, and therefore, the reluctance towards it will also be less.
The Kaizen philosophy is used in globally recognized organizations such as Toyota, Samsung or Nestlé, generating greater productivity on the part of their employees, followed by continuous improvement in their activities and the fulfillment of goals and objectives.
What does it mean?
The term Kaizen is made up of two Japanese words: kai (change) and zen (better), continuous improvement. It is said that the meaning of Kaizen derives from two fundamental pillars: graduality and continuity.
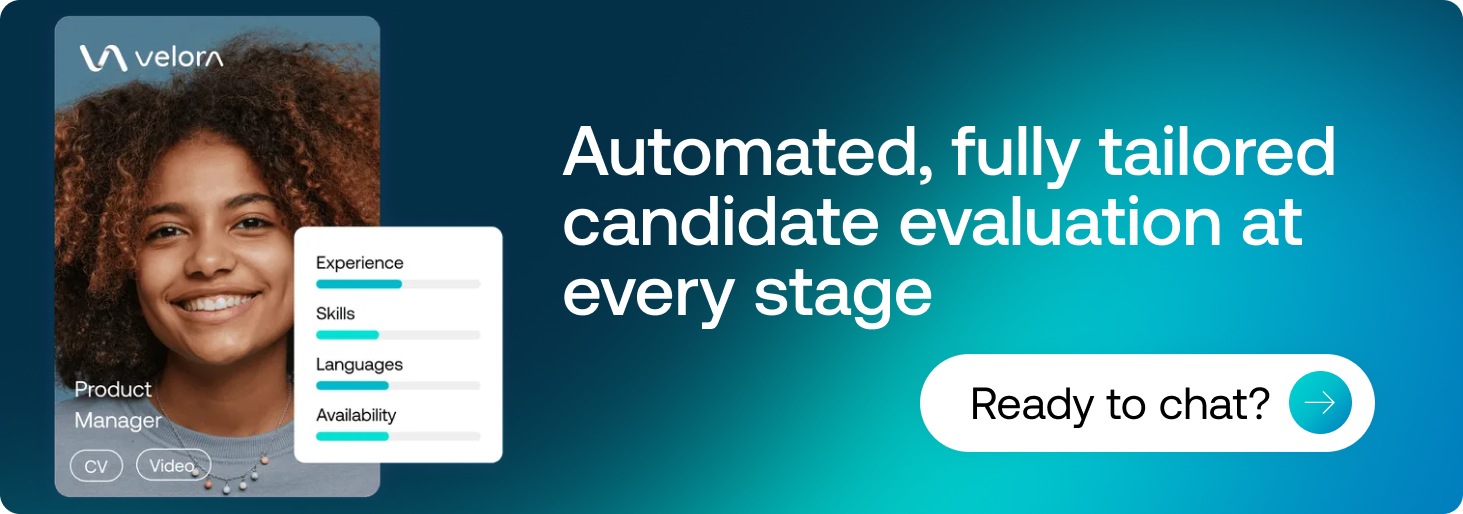
The 5'S of the Kaizen Method
It consists of Japanese words that, in an orderly manner, offer a step by step to implement this discipline:
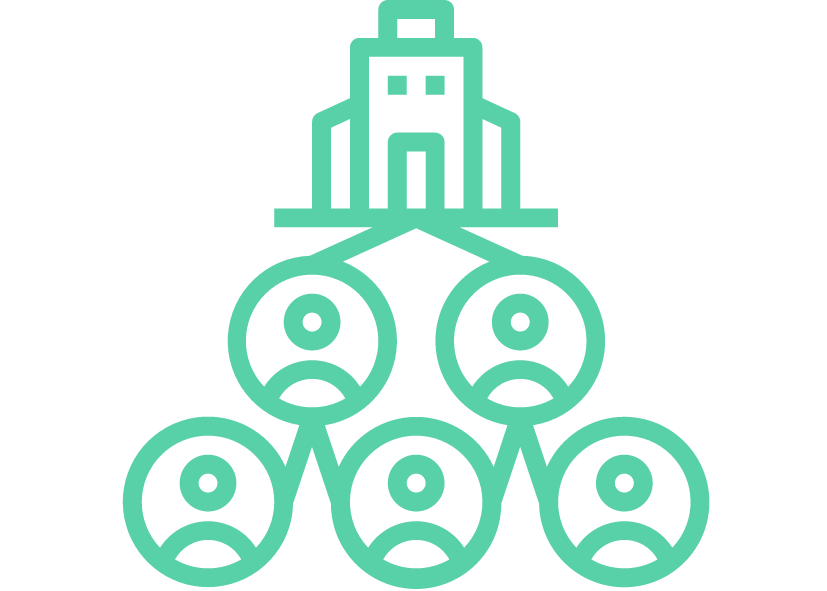
Organization — Seiri
This concept focuses on the organization of the elements that the company can make, in order to make a distinction between those parts that are indispensable for production and those that do not provide any value
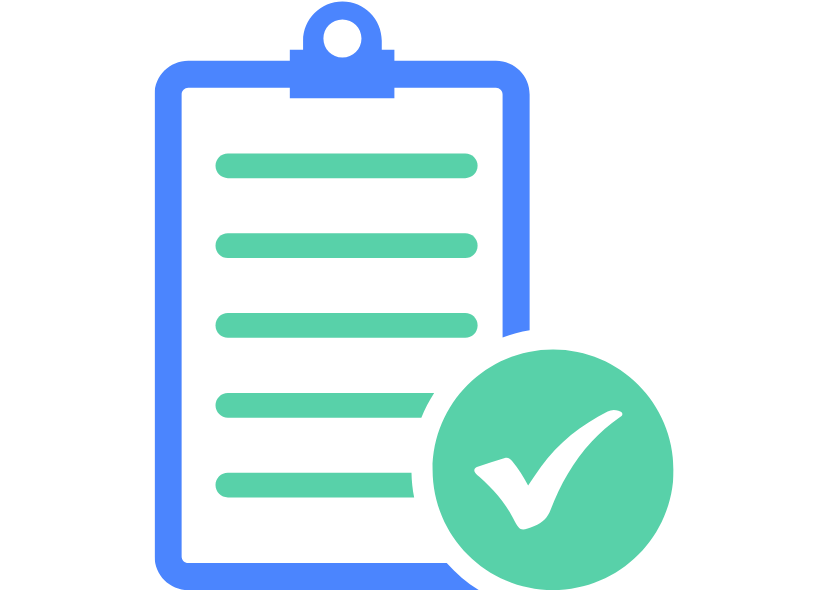
Order — Seiton
It is a matter of making lists with the positive parts that we have been identifying throughout the previous point. The objective is to have an outline of all the essential tasks in our process and that they are all duly identified.
In this way, we will no longer have to use resources in the future to find them, since it is a job that we will have done previously.
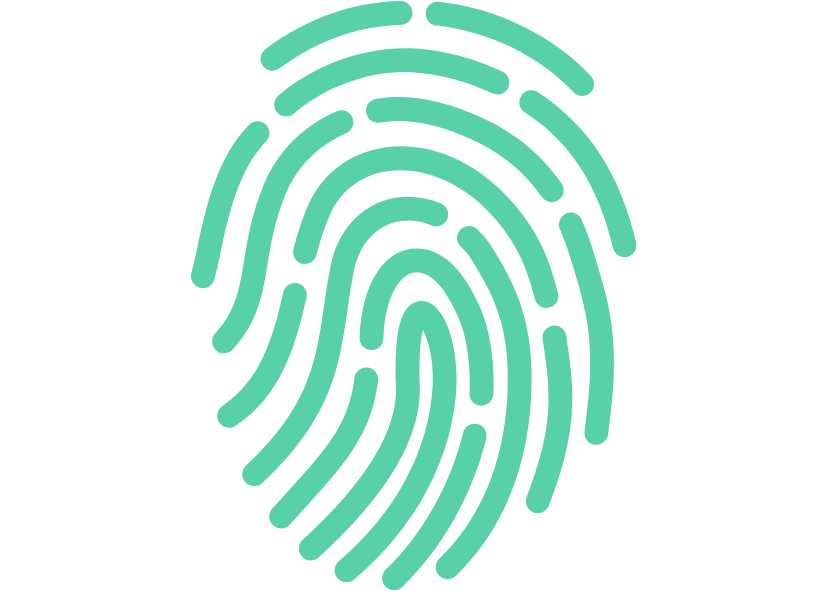
Identification — Seisō
This is the point at which we will find possible errors or ineffective forms of action within our company's production system. It's not just about identifying them, the important thing is finding a solution for each of them.
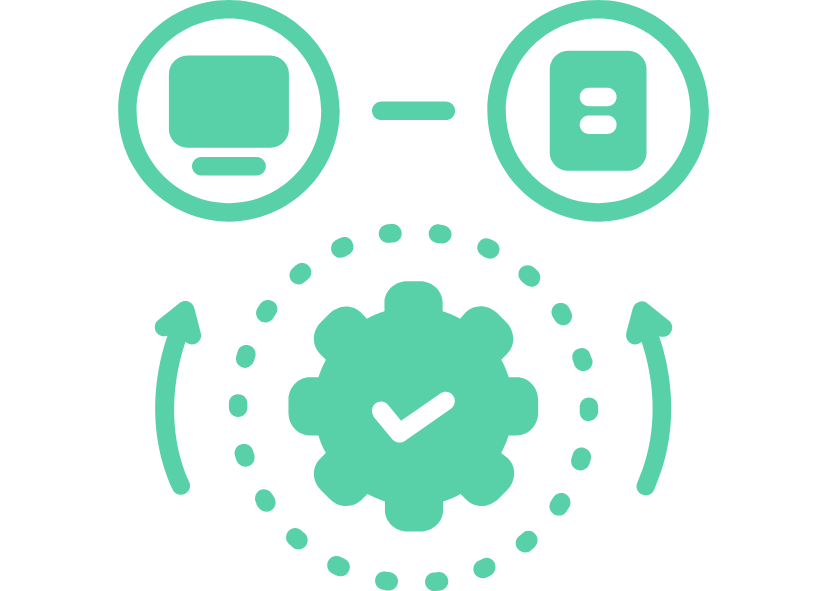
Standardization — Seiketsu
After completing the previous steps, it's time to establish rules and procedures so that all employees are moving in the same direction.
This standardization process will facilitate work, so that all employees enjoy the appropriate work environment and can thus form a competitive team. The fact is that a company can only reach the top if it has the right tools for it.
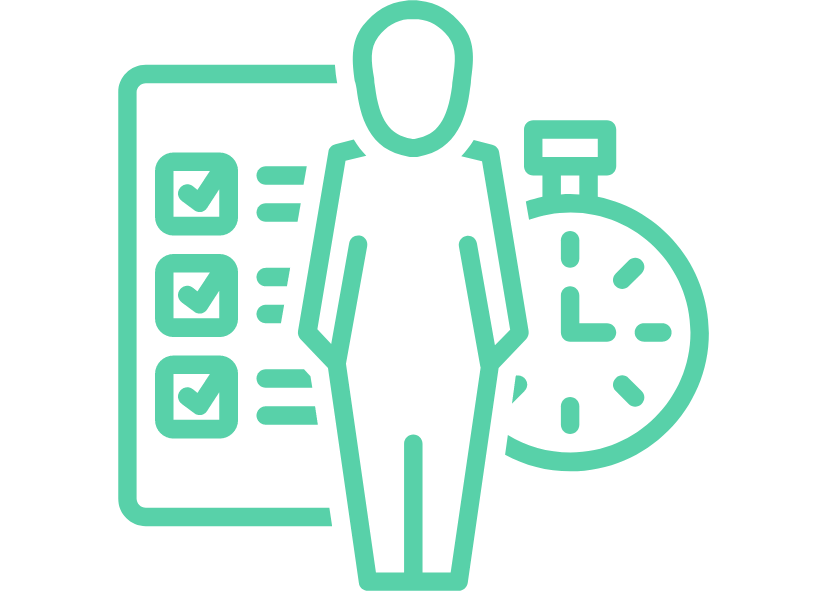
Self-Discipline — Shitsuke
This point refers to the commitment that all members of the organization must make with the methodology. The objective is to make the “five S” method and techniques a habit.
The PDCA cycle or Deming circle
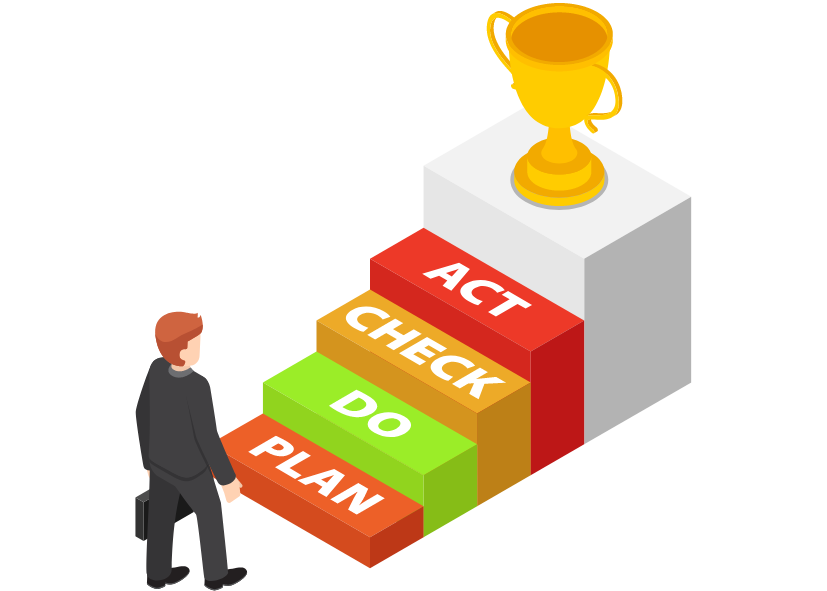
William Deming was responsible for promoting this technique, which is based on a cycle consisting of four phases.
Plan (Plan): The first stage of any project consists of analyzing the state of our company and setting clear and attainable goals.
Do (Do): implement the defined plan based on an execution schedule organized by priorities.
Check: It is a fundamental stage of the cycle, by measuring the achievement of the objectives we will know if we are progressing according to what has been estimated and if not, to be able to correct errors. There are control tools such as the Pareto chart, Check lists and performance metrics (KPIs).
Act: apply the appropriate corrective measures and study their results with the objective of creating a new, more efficient and productive plan of action
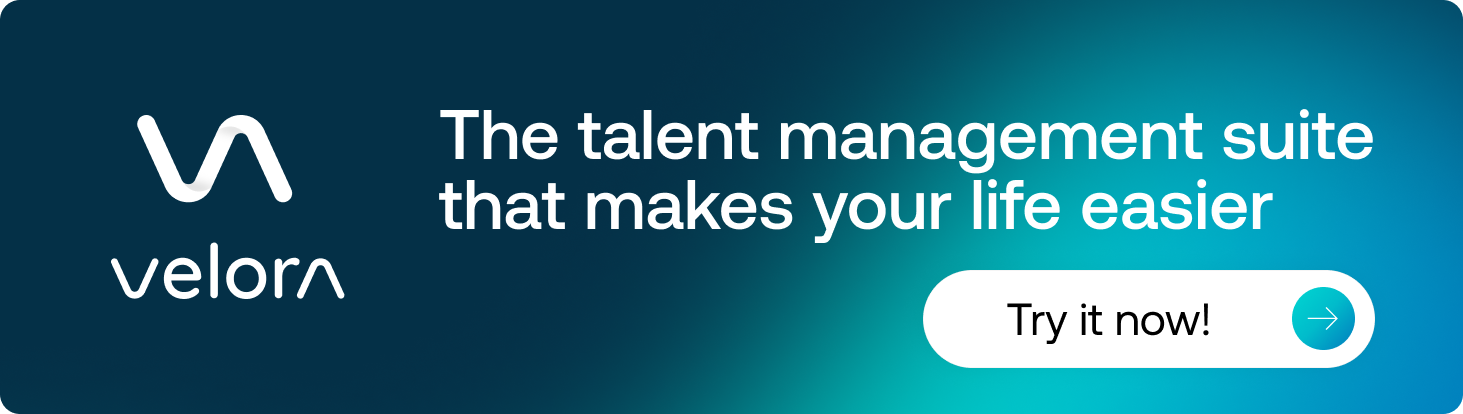
Steps to implement it
The Kaizen method must be applied to all employees of an organization in a general way, only by working as a team towards the same direction, will they achieve their objectives. In addition, the company must carry out the process, continuously inform itself about the current state of the company, personally evaluate the situation and guide people in it.
To implement the Kaizen Method, it is necessary to follow these points:
Standardization: application of the process in a safe and easy way so that employees can do it productively and ensure that they deliver a quality service that meets customer expectations.
Internal Management: This factor refers to the “five S”, which means organizing and achieving better results through motivation.
Eliminate waste: All activities that do not include added value should be discarded.
The level of competition is increasing every day thanks to technological progress. That's why companies need to increase the quality of their services and solve problems effectively. The Kaizen Method is about continuously improving and eliminating all the elements that slow down the process, until reaching the state of total perfection.
Calculate your potential savings in selection
Get instantly and free of charge the savings in time and resources that you can achieve in your selection
.png)
Related articles
More articles to inspire your HR strategy